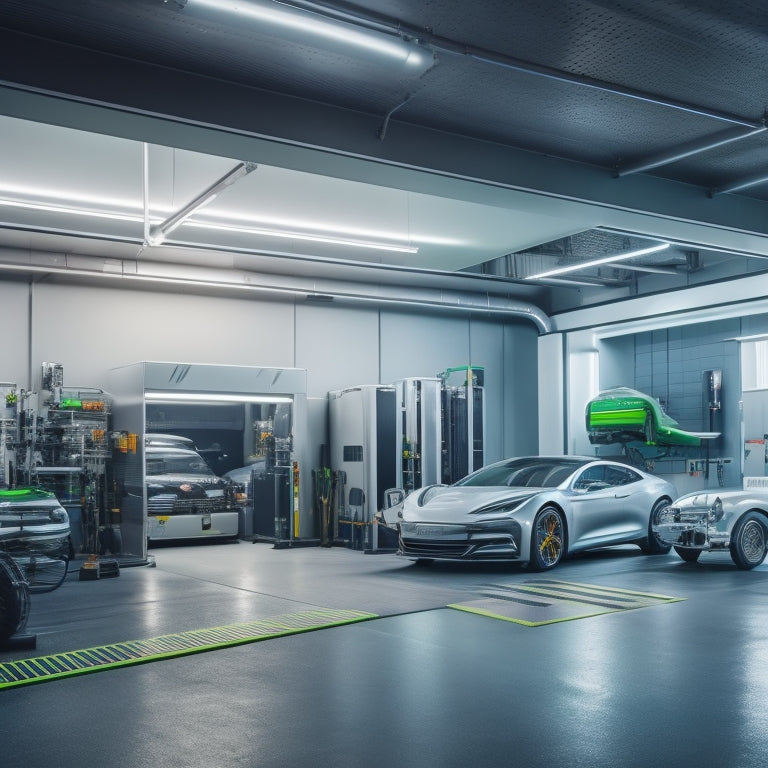
10 Essential Fleet Maintenance Tips for Optimal Energy
Share
To maintain your fleet's peak energy efficiency, adopt a proactive maintenance strategy combining regular cleaning and monitoring, electrical system inspections, and panel maintenance to minimize energy consumption and maximize output. Regularly clean and monitor your fleet to identify inefficiencies and optimize energy usage. Inspect electrical systems for damage, check connections monthly, and conduct thermal imaging checks. Track energy consumption, guarantee proper panel cooling, and update software and firmware. By following these essential tips, you'll reduce energy consumption, extend equipment lifespan, and improve overall fleet performance - and that's just the starting point for tapping into your fleet's full potential.
Key Takeaways
• Regular cleaning and monitoring of energy systems helps track consumption patterns and identify inefficiencies for optimal energy efficiency.
• Conducting electrical system inspections and voltage drop analysis helps prevent corrosion and ensures peak performance.
• Maintaining proper panel angles and tracking adjustments maximize energy production and prevent overheating.
• Tracking energy consumption through fuel logs and odometer readings helps identify areas for improvement and reduces costs.
• Scheduling regular inspections with certified experts prevents downtime, ensures reliability, and contributes to sustainable fleet operations.
Schedule Regular Cleaning Sessions
By incorporating regular cleaning sessions into your maintenance routine, you can prevent the buildup of dirt and debris that can decrease your fleet's energy efficiency. A well-maintained fleet not only reduces energy consumption but also guarantees safety on the road.
To optimize energy efficiency, it's important to establish a cleaning frequency that suits your fleet's specific needs. Depending on the operating environment, you may need to clean your vehicles daily, weekly, or monthly. For instance, if your fleet operates in areas with high levels of pollution or harsh weather conditions, you may need to clean them more frequently.
Effective soil removal is crucial in maintaining your fleet's energy efficiency. Dirt and debris can accumulate on vital components, such as air filters, radiators, and engine compartments, leading to increased energy consumption. By removing soil and debris regularly, you can ensure that your fleet operates at its best, reducing energy waste and promoting a safer, more efficient operation.
Monitor Energy Output Daily
As you monitor energy output daily, you'll want to track energy consumption patterns to identify areas for improvement.
By analyzing daily performance, you can pinpoint inefficiencies and optimize energy usage.
With real-time data monitoring, you'll have the insights needed to make informed decisions and maximize your fleet's energy efficiency.
Energy Output Tracking
Tracking energy output daily helps you identify trends, patterns, and anomalies that can greatly impact your fleet's overall energy efficiency. By monitoring energy output daily, you can make data-driven decisions to optimize your fleet's energy performance. This involves tracking key performance indicators such as energy consumption, fuel efficiency, and power output.
Here are some benefits of daily energy output tracking:
-
Improved Energy Forecasting: Accurate energy output tracking enables you to forecast energy demand, reducing the risk of grid capacity overload and promoting a more stable energy supply.
-
Enhanced Grid Capacity: By identifying areas of high energy consumption, you can optimize energy distribution and reduce strain on the grid, ensuring a more efficient and reliable energy supply.
-
Increased Safety: Daily energy output tracking helps you identify potential safety risks, such as electrical faults or equipment malfunction, allowing you to take proactive measures to prevent accidents and maintain a safe operating environment.
Daily Performance Analysis
Your daily performance analysis should involve scrutinizing energy output data to pinpoint areas of improvement, identify trends, and optimize fleet performance. By doing so, you'll be able to identify patterns and anomalies that may indicate potential energy waste or inefficiencies. This analysis is vital in maintaining peak energy output and guaranteeing the safety of your fleet.
Aspect | Action |
---|---|
Energy Fluctuations | Analyze energy output data to identify unusual spikes or dips |
Operational Trends | Identify patterns in energy usage to optimize fleet performance |
Energy Inefficiencies | Pinpoint areas of energy waste and implement corrective measures |
Performance Optimization | Adjust energy output to enhance fleet performance and safety |
Through daily performance analysis, you'll be able to detect energy fluctuations, identify operational trends, and pinpoint areas of energy inefficiencies. By taking corrective action, you'll optimize your fleet's performance, reduce energy waste, and ensure the safety of your fleet. By making this analysis a daily habit, you'll be able to stay on top of your fleet's energy output and make data-driven decisions to enhance performance.
Real-Time Data Monitoring
You can stay ahead of potential energy efficiency issues by monitoring your fleet's energy output in real-time, allowing you to respond swiftly to anomalies and optimize performance.
With real-time data monitoring, you'll be able to identify areas of inefficiency and take corrective action before they escalate into major problems. This proactive approach guarantees your fleet operates at peak performance, reducing downtime and energy waste.
By leveraging advanced technologies like data visualization and predictive analytics, you'll gain a deeper understanding of your fleet's energy usage patterns.
This insights-driven approach enables you to:
- Pinpoint energy-intensive operations and optimize them for maximum efficiency
- Detect potential equipment failures before they occur, reducing downtime and repair costs
- Make data-driven decisions to optimize your fleet's energy output and reduce your environmental footprint
Inspect Panels for Damage
Regular visual inspections of solar panels are essential to identify damage that can compromise energy output and overall system efficiency. As a fleet manager, you know that panel durability and weather resistance are vital to maintaining peak energy production. During your inspections, look for signs of physical damage, such as cracks, dents, or broken glass. Also, check for signs of weather-related damage, like corrosion, rust, or fading.
Common Damage Types | Inspection Tips |
---|---|
Cracks and breaks | Inspect panel frames and glass for signs of cracks or breaks |
Corrosion and rust | Check mounting hardware and frames for signs of corrosion or rust |
Fading and discoloration | Inspect panels for signs of fading, discoloration, or delamination |
Remember to inspect panels during different weather conditions to identify potential issues. By catching damage early, you can prevent energy losses and ensure your fleet operates at peak performance.
Check Electrical Connections Monthly
When you check electrical connections monthly, you're ensuring the peak performance of your fleet's energy system.
You'll want to verify the integrity of connections, prevent corrosion, and analyze voltage drops to minimize energy losses.
Connection Integrity Check
Monthly inspections of electrical connections guarantee that your fleet's electrical systems operate within peak energy parameters. You can't afford to overlook this essential maintenance task, as faulty connections can lead to equipment failure, downtime, and even safety hazards.
By checking electrical connections regularly, you make sure that your fleet operates efficiently and safely.
When conducting a connection integrity check, remember to:
- Inspect cables for signs of wear, damage, or corrosion, and perform cable inspections to identify potential issues before they escalate.
- Conduct wire testing to verify the integrity of electrical connections and identify any weaknesses.
- Verify that all connections are secure, clean, and free of debris to prevent electrical arcing and shorts.
Corrosion Prevention Methods
To prevent corrosion from compromising your fleet's electrical connections, you should apply a thin layer of dielectric grease to all connectors and terminals, guaranteeing a secure, waterproof seal. This proactive measure will safeguard your fleet's electrical integrity and prevent costly repairs down the line.
When selecting materials for your electrical connections, prioritize corrosion-resistant options like stainless steel, aluminum, or coated copper. These materials will provide an added layer of protection against moisture and environmental factors that can accelerate corrosion.
In addition to dielectric grease, explore coating options like silicone or polyurethane-based coatings, which offer excellent corrosion protection and can be applied to connectors, terminals, and cables.
Regularly inspecting and cleaning electrical connections will also help prevent corrosion. By taking these preventative measures, you'll significantly lower the risk of corrosion-related issues and ensure your fleet operates safely and efficiently.
Voltage Drop Analysis
Performing a voltage drop analysis on your fleet's electrical connections every month helps identify potential issues before they escalate into costly problems. This proactive approach guarantees your fleet operates efficiently, reducing energy losses and minimizing downtime.
By conducting regular voltage drop analysis, you'll be able to:
-
Identify areas of high energy losses, allowing you to take corrective action to reduce waste and optimize energy consumption
-
Create a voltage map of your fleet's electrical system, highlighting areas prone to voltage drops and energy losses
-
Pinpoint potential safety hazards, such as overheated connections or electrical surges, and take corrective action to prevent accidents
Perform Thermal Imaging Checks
You can identify potential electrical faults and energy losses in your fleet's electrical systems by conducting regular thermal imaging checks. This proactive approach helps you detect anomalies before they escalate into safety hazards or costly repairs.
Thermal imaging, also known as infrared analysis, involves capturing heat maps of your electrical systems to identify areas of excessive heat generation. This heat mapping technique is particularly useful for monitoring electrical connections, switchgear, and other components prone to overheating.
Maintain Proper Panel Angles
When maintaining your fleet's solar panels, you'll want to make sure you're getting the most energy out of them, and that starts with maintaining proper panel angles.
You'll need to calculate the best tilt for your panels, as well as make adjustments to the angle throughout the year to account for seasonal changes.
Optimal Tilt Calculation
To maximize energy production, calculating the ideal tilt angle for your solar panels is crucial, as even slight deviations can greatly impact overall system efficiency. You want to make sure your panels are angled to capture the most sunlight possible, but improper tilt angles can lead to reduced energy output and even panel damage.
When calculating the best tilt angle, consider the following key factors:
-
Tilt Variations: Account for seasonal changes in the sun's position to optimize energy production throughout the year.
-
Shadow Analysis: Identify potential shade sources, such as trees or buildings, to adjust the tilt angle and minimize energy losses.
-
Regional Climate: Consider local climate conditions, including wind and snow loads, to make certain your panels can withstand environmental stresses.
Panel Angle Adjustments
By maintaining your solar panels at the best angle, you'll maximize energy production and prevent potential damage from improper alignment. Proper panel angles are essential for preserving the structural integrity of your solar fleet. When panels are angled correctly, they can withstand harsh weather conditions, including strong winds, without compromising their performance.
Improper alignment can lead to reduced energy output, premature wear, and even catastrophic failures. To guarantee peak energy production, adjust your panels to account for wind resistance, considering local wind patterns and speeds. Regularly inspect your panels to detect any signs of misalignment, which can be caused by settlement or foundation shifts. Correcting these issues promptly will prevent further damage and ensure your solar fleet operates at its best.
Seasonal Angle Changes
As the seasons change, adjust your solar panels' angles to optimize energy production, making sure you're capturing the most energy from the sun's varying position in the sky. This important step will greatly impact your energy output, and it's vital to get it right.
During winter, adjust your panels to a steeper angle to capture the low-angled winter sun, maximizing energy production during this time. This is especially important for regions with heavy snowfall, as Winter Reflections can reduce energy output.
Here are some key takeaways to keep in mind:
-
In the summer, optimize your panels for a shallow angle to accommodate the high-angled sun, ensuring maximum energy production during the Summer Orientation.
-
Regularly inspect your panels to ensure they're free from debris and obstacles that may hinder energy production.
-
Keep a maintenance log to track your adjustments and energy output, helping you identify areas for improvement and optimize your energy production over time.
Keep Track of Energy Consumption
You monitor energy consumption by regularly reviewing fuel logs, odometer readings, and engine performance data to identify areas of inefficiency. This helps you understand your fleet's energy usage patterns and make informed decisions to optimize energy consumption.
Conducting regular energy audits is essential to identify opportunities for improvement. By analyzing your fleet's energy consumption patterns, you can pinpoint areas where energy is being wasted and take corrective measures. For instance, you may discover that certain routes or driving habits are leading to excessive fuel consumption. With this data, you can implement changes to reduce energy waste and improve overall efficiency.
Ensure Proper Panel Cooling
Proper panel cooling is essential to preventing overheating, which can lead to reduced energy efficiency, increased maintenance costs, and even premature component failure. By ensuring proper panel cooling, you're not only prolonging the lifespan of your equipment, but also maintaining peak energy efficiency.
Here are some important considerations to keep in mind:
-
Heat Sink Design: A well-designed heat sink can greatly improve heat dissipation, reducing the risk of overheating. Make sure that your heat sink design is optimized for your specific equipment and operating conditions.
-
Cooling System Optimization: Regularly inspect and maintain your cooling system to ensure it's operating at its best. This includes cleaning or replacing air filters, checking coolant levels, and inspecting for signs of wear and tear.
-
Monitoring Temperature: Continuously monitor your equipment's temperature to catch any potential issues before they escalate. This allows you to take proactive measures to prevent overheating and maintain peak energy efficiency.
Update Software and Firmware
What's the impact of outdated software and firmware on your fleet's energy efficiency, and are you taking the necessary steps to mitigate it?
Failing to update your software and firmware can lead to decreased energy efficiency, reduced performance, and increased cybersecurity risks. Outdated systems can be vulnerable to hacking, allowing unauthorized remote access to your fleet's systems. This can compromise your entire operation, putting your fleet and personnel at risk.
Regularly updating your software and firmware guarantees you have the latest security patches, features, and optimizations. This helps prevent cyber threats and guarantees your systems run smoothly and efficiently. You'll also benefit from improved performance, increased energy efficiency, and reduced downtime.
Make it a habit to check for updates regularly, and prioritize implementing them as soon as possible. By doing so, you'll minimize the risk of cybersecurity breaches and ensure your fleet operates at peak energy efficiency. Don't wait until it's too late – stay ahead of potential issues by keeping your software and firmware up to date.
Conduct Annual Professional Inspections
During annual professional inspections, a trained expert will scrutinize your fleet's entire system to identify and address potential energy-wasting issues before they escalate into major problems. This proactive approach guarantees that your fleet operates at peak energy efficiency, reducing energy consumption and costs.
Regular inspections also help extend the lifespan of your equipment and prevent unexpected downtime.
To get the most out of your inspections, make sure to:
- Schedule inspections at a frequency that aligns with your fleet's usage and manufacturer recommendations
- Only work with experts certified in your specific fleet type and equipment
- Request a detailed report outlining findings, recommendations, and completed repairs.
Frequently Asked Questions
How Often Should I Replace Worn-Out Electrical Connections?
'Remember the 2018 electric bus fire in California, caused by faulty connections? You should replace worn-out electrical connections every 6-12 months, or upon cable inspection revealing damaged insulation, and always conduct connection testing to guarantee safe operations.'
Can I Clean Solar Panels During Peak Sun Hours?
When cleaning solar panels, avoid peak sun hours to prevent water evaporation, which can leave streaks and reduce panel efficiency. Instead, clean during early morning or late afternoon to minimize dust accumulation and guarantee maximum energy harvesting.
What Is the Ideal Temperature for Optimal Solar Panel Performance?
When you're optimizing solar panel performance, you'll want to keep temperatures between 59°F and 95°F (15°C and 35°C) for maximum efficiency, as excessive heat can reduce efficiency by up to 20%, and high heat resistance can boost efficiency.
How Do I Troubleshoot Low Energy Output Issues Quickly?
When troubleshooting low energy output issues, you'll want to conduct energy audits to identify inefficiencies, then perform a thorough fault analysis to pinpoint the root cause, ensuring a safe and efficient solution.
Are Annual Professional Inspections Really Necessary for Small Fleets?
You might think skipping annual professional inspections saves your small fleet money, but consider the long-term risks: even a small fleet size can lead to significant inspection cost savings and guarantee safety on the road.
Related Posts
-
7 Best Home Hydrogen Fuel Cells for Clean Power
You're considering adopting hydrogen fuel cells for clean power at home, but you want to know the best options. Reput...
-
3 Green HVAC Filters for Solar-Powered Homes
When outfitting your solar-powered home with an HVAC system, you'll want to choose filters that align with your commi...
-
7 Smart Air Purification Hacks for Energy-Savvy Homes
You can notably improve your indoor air quality while minimizing energy consumption by implementing strategic air pur...